Dvigubos sijos tiltinis kranas, naudojamas orlaivio fiuzeliažo korpuso komponentams tvarkyti
The factory of the aircraft body shell component supplier is located in Nordenham, Germany. This factory specializes in producing aluminum integral aircraft body casings. Carbon fiber composite material body structures can also be manufactured for assembling complete body structures. Mainly used for large civil aviation aircraft. The factory needs to produce over 5000 body shell components annually. So SEVENCRANE's dvigubos sijos tiltinis kranas and KBK crane were chosen as aerial conveying equipment. To efficiently transport the body shell components to various workstations and freight car compartments in the production workshop.
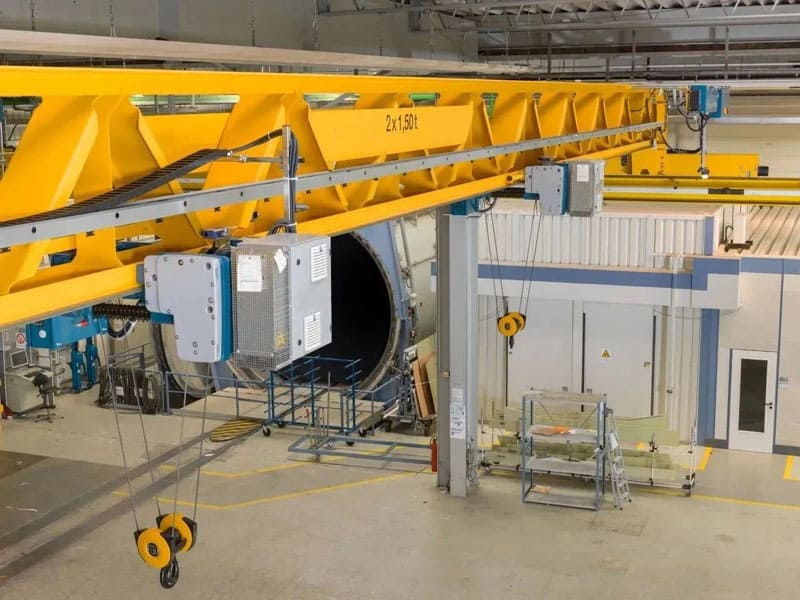
The user's production workshop has installed two bridge cranes with a span of 24 meters. Each crane is equipped with two 1.5 ton load wire rope electric hoists. Which operate on a 115 meter long workshop track to lift various components of the aircraft body shell during the production process. These two cranes can be linked and controlled, and the four wire rope electric hoists can operate under synchronous control. After two bridge cranes operate within a distance of 4 meters, the operator can press the button on the control handle to switch to linkage control. Control four wire rope electric hoists on two cranes to accurately and synchronously lift and lift large components of the aircraft fuselage shell. The four wire rope electric hoists are all frequency controlled, allowing operators to accurately locate large components of the body shell when handling.
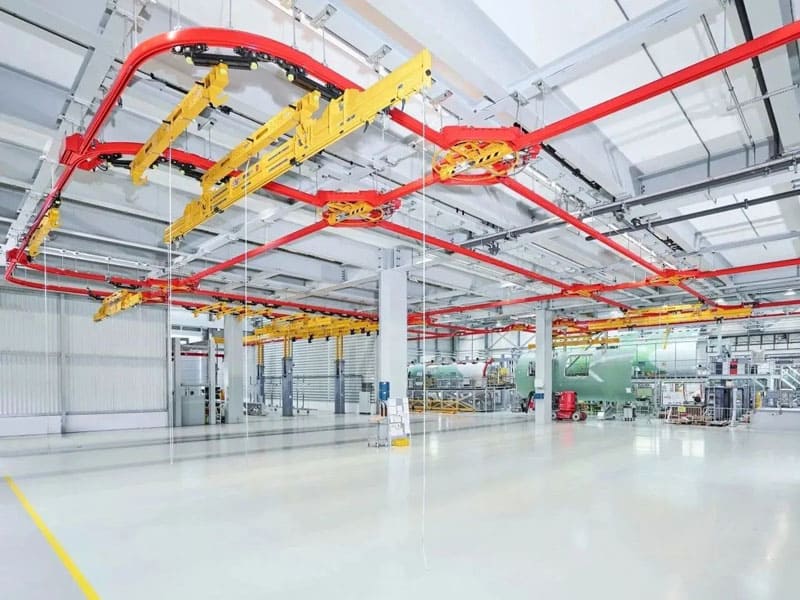
The load capacity of KBK modular lightweight crane system can reach 3200 kilograms. The KBK crane system has a wide range of components. And can customize material handling plans according to specific user requirements. It can flexibly cover linear areas and is often used for material handling in linear assembly lines. Its biggest feature is the ability to flexibly adapt to various on-site environments. Without being limited by any pillars, door frames, turning angles, etc.