Vindforebyggende foranstaltninger til portalkran
As a large-scale mechanical device, gantry crane is often exposed to strong winds. This can potentially cause damage and disrupt their operation. Therefore, it is important to implement effective measures to prevent wind damage to gantry crane.
One of the most common methods for wind protection is to install windshields in the area where the machine is located. Windshields can be made of various materials, such as metal or glass. And may be stationary or adjustable to accommodate different wind directions and speeds. They can help reduce the impact of wind on the gantry crane by blocking or diverting the wind flow.
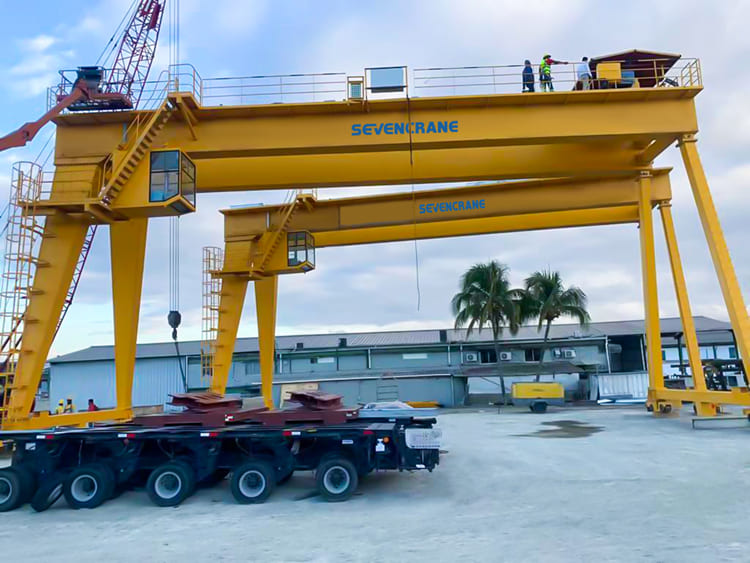
Another approach is to increase the weight or stability of it. This can be achieved by using heavier materials for the portalkran construction, adding counterweights. Or anchoring the gantry crane firmly to the ground. A heavier crane is less likely to be pushed or toppled over by strong gusts of wind.
Furthermore, some gantry cranes are equipped with sensors or detectors that can detect changes in wind speed and direction. These sensors can trigger alarms to alert operators to take appropriate precautions. For example, adjust the position of the crane or activate the emergency shutdown mechanism to prevent wind damage.
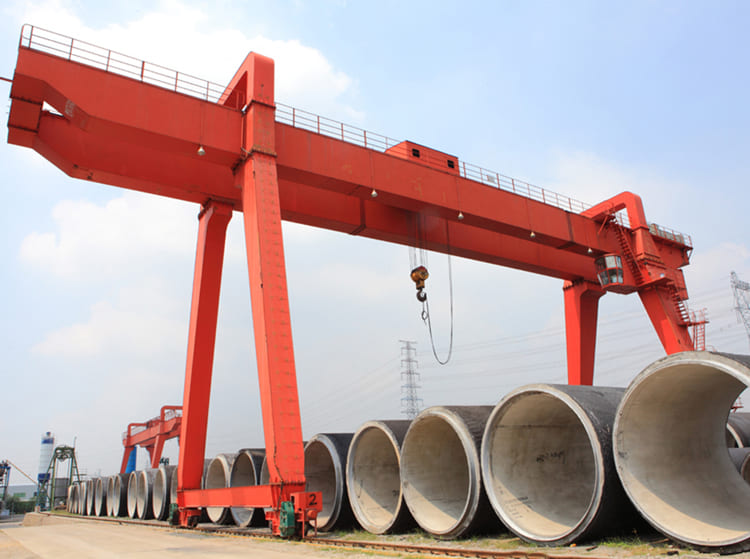
In addition, regular maintenance and inspection are crucial to ensure their proper functioning and minimize the risk of wind damage. This includes checking for signs of wear and tear, corrosion, or loose parts that could be vulnerable to wind stress, and repairing or replacing them as needed.
Finally, it is important to have a contingency plan in place in case of severe weather conditions. This may involve temporarily shutting down the portalkran, evacuating personnel from the area, or implementing emergency procedures to minimize the risk of damage or injury.
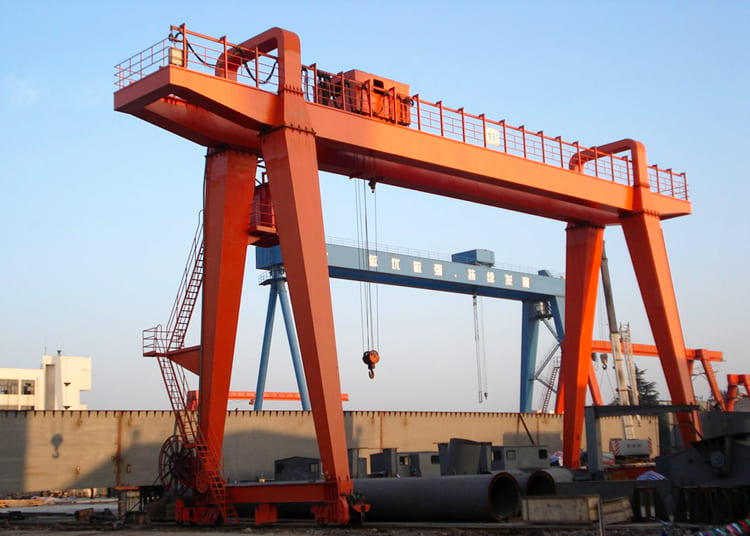
Overall, preventing wind damage to gantry cranes requires a combination of proactive measures, such as installing windshields and increasing gantry crane stability, as well as reactive responses, such as sensors and contingency plans. By implementing these measures, the safety of the operators is ensured and downtime is minimised.